Evolution of Automation in Self-Loading Concrete Mixers: Revolutionizing Construction Efficiency
- blog016
- Jan 31, 2024
- 3 min read
In the dynamic landscape of construction, innovation continually reshapes traditional practices, driving efficiency and productivity to new heights. Among the remarkable advancements, the integration of a high degree of automation in self-loading concrete mixers stands as a pivotal evolution in modern construction equipment. This article delves into the transformative impact of automation in self-loading concrete mixers, elucidating its benefits, technological facets, and implications for the construction industry.
Embracing Automation: Redefining Concrete Mixing Dynamics
At the heart of construction projects, concrete serves as the cornerstone, providing structural integrity and durability to diverse infrastructures. The conventional concrete mixing process, characterized by manual labor and inherent limitations, has long necessitated innovation to meet the escalating demands of modern construction projects.
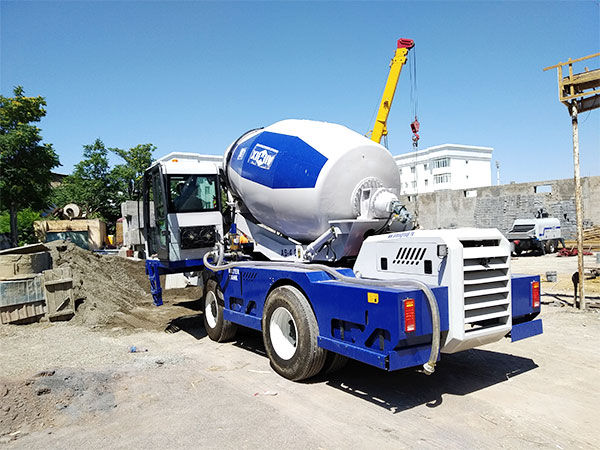
Enter the era of automated self loading cement mixer, heralding a paradigm shift in concrete mixing dynamics. These innovative machines embody a fusion of cutting-edge technology and engineering prowess, revolutionizing the efficiency, accuracy, and safety of concrete production.
Technological Marvels: Unveiling the Automation Arsenal
The essence of automation in self-loading concrete mixers lies in its multifaceted technological arsenal, encompassing a spectrum of innovative features designed to streamline and optimize the concrete mixing process:
1. Automated Loading Systems: Central to automation, automated loading systems meticulously calibrate and dispense aggregates, cement, water, and additives into the mixing drum with precision and consistency. By eliminating manual intervention, these systems ensure optimal material proportions, enhancing the quality and uniformity of the concrete mix.
2. Batching and Mixing Controls: Leveraging sophisticated electronic sensors and programmable logic controllers (PLCs), batching and mixing controls orchestrate the mixing process with unparalleled accuracy. Real-time monitoring and adjustment of mixing parameters empower operators to achieve optimal mix designs tailored to specific project requirements.
3. Intelligent Dispensing Mechanisms: Water and additive dispensing mechanisms epitomize the intelligence of automation, meticulously regulating the flow and dosage of water and additives into the mixing drum. By adhering to predetermined mix designs, these mechanisms uphold the integrity and performance of the concrete mix, even in the face of fluctuating environmental conditions.
4. Self-Adjusting Algorithms: In a testament to ingenuity, self-adjusting algorithms dynamically optimize the mixing process in response to evolving environmental variables. From ambient temperature fluctuations to aggregate characteristics, these algorithms fine-tune mixing parameters, ensuring consistent quality and performance across diverse operating conditions.
5. Remote Monitoring and Control: Harnessing the power of connectivity, remote monitoring, and control functionalities empower operators to oversee the mixing process and intervene promptly, irrespective of geographical constraints. Through intuitive interfaces accessible via mobile devices or computers, operators exercise unprecedented control and visibility, enhancing operational efficiency and responsiveness.
6. Safety Protocols and Fail-Safes: Automation underscores a commitment to safety, integrating robust safety protocols and fail-safe mechanisms to mitigate risks and safeguard personnel and equipment. From emergency stop mechanisms to overload protection systems, these features instill confidence in operators, fostering a culture of safety and reliability.

Implications for the Construction Landscape: Paving the Path to Progress
The integration of a high degree of automation in self-loading concrete mixers reverberates throughout the construction landscape, catalyzing a cascade of transformative effects:
1. Enhanced Efficiency and Productivity: Automation augments operational efficiency, expediting the concrete mixing process and minimizing downtime. With streamlined workflows and optimized resource utilization, construction timelines compress, accelerating project delivery without compromising quality.
2. Precision and Consistency: By automation, the variability inherent in manual labor dissipates, replaced by the unwavering precision and consistency of machine-driven processes. From batch to batch, concrete quality remains steadfast, meeting stringent performance criteria and regulatory standards.
3. Labor Optimization and Skill Upgradation: Automation liberates labor from mundane tasks, enabling personnel to focus on higher-value activities that demand human expertise and creativity. Moreover, as automation proliferates, the demand for skilled operators adept in navigating technologically advanced equipment burgeons, ushering in a new era of professional development and specialization.
4. Sustainability and Environmental Stewardship: Through optimized resource utilization and waste reduction, automation champions sustainability, mitigating the environmental footprint of concrete production. By curbing material wastage and energy consumption, construction practices align with principles of environmental stewardship, fostering a harmonious coexistence with the planet.
Conclusion: Pioneering the Future of Concrete Construction
In the annals of construction history, the advent of automation in mini self loading concrete mixer emerges as a transformative milestone, heralding a new era of efficiency, precision, and sustainability. As technology continues to evolve and permeate every facet of construction, the journey toward innovation-driven progress beckons, promising boundless opportunities for advancement and excellence. In the crucible of automation, the future of concrete construction unfolds, propelled by the relentless pursuit of excellence and the indomitable spirit of innovation.
Comments