Ensuring Safety in the Operation of Aggregate Crushers: Best Practices and Protocols
- blog016
- Jan 15, 2024
- 3 min read
Aggregate crushers play a pivotal role in the construction industry, facilitating the production of essential materials for infrastructure projects. As with any industrial machinery, the operation of aggregate crushers comes with inherent safety concerns. This article explores the key practices and protocols implemented to ensure the safety of personnel and equipment during the operation of aggregate crushers.
Operator Training and Education:
A cornerstone of safety in aggregate crusher operations is comprehensive operator training and education. Operators must be well-versed in the safe and proper operation of the specific aggregate crusher they are working with. This includes understanding the controls, emergency procedures, and potential hazards associated with the machinery.
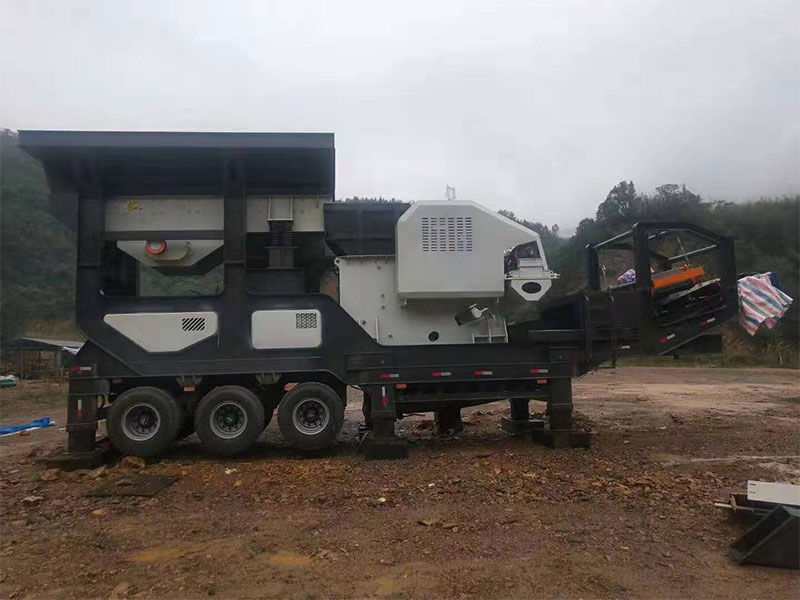
Safety Protocols and Standard Operating Procedures:
Establishing and enforcing safety protocols and standard operating procedures (SOPs) is crucial for minimizing risks. These protocols should outline safe start-up and shut-down procedures, material feeding guidelines, and emergency response plans. Regular training sessions and reviews of these protocols help reinforce a culture of safety among operators.
Personal Protective Equipment (PPE):
Wearing appropriate personal protective equipment is a non-negotiable aspect of safety. Operators working with aggregate crushers should use PPE such as hard hats, steel-toed boots, safety glasses, ear protection, and dust masks as required. The specific PPE may vary based on the crusher type and the nature of the materials being processed.
Equipment Inspection and Maintenance:
Regular inspection and maintenance of aggregate crushers are paramount for preventing equipment malfunctions and reducing the risk of accidents. This includes checking for wear on crusher components, inspecting belts and conveyor systems, and ensuring that safety guards are in place and functional. Any identified issues should be promptly addressed to maintain optimal safety.
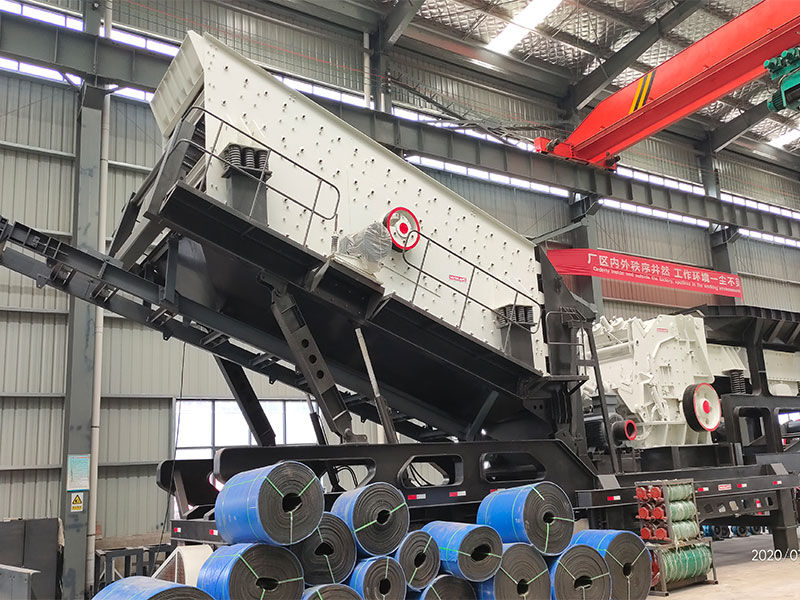
Emergency Stop Systems:
Aggregate crushers are equipped with emergency stop systems that allow operators to quickly shut down the machinery in case of an emergency. This feature provides an immediate response to potential hazards and ensures the safety of personnel working around the crusher.
Isolation of Energy Sources:
Before performing maintenance or repairs on aggregate stone crusher machine plants, it is essential to isolate energy sources to prevent accidental start-ups. Lockout/tagout procedures should be followed diligently, ensuring that all energy sources are secured before any maintenance activities are initiated.
Dust Control Measures:
Dust generated during the crushing process can pose respiratory and environmental hazards. Effective dust control measures, such as dust suppression systems and proper ventilation, should be implemented. Operators must also use dust masks when working in areas with high dust levels to protect their respiratory health.
Communication and Signage:
Clear communication is vital in a crusher operation environment. Signage indicating restricted areas, safety protocols, and emergency contact information should be prominently displayed. Additionally, effective communication among team members through radios or other communication devices enhances overall safety awareness.
Regular Safety Audits and Inspections:
Conducting regular safety audits and inspections is a proactive approach to identifying potential hazards and ensuring compliance with safety standards. These audits should encompass both equipment checks and the observation of operator practices, allowing for continuous improvement in safety protocols.
Continuous Training and Improvement:
Safety is an ongoing commitment that requires continuous training and improvement. Staying informed about advancements in safety technologies and industry best practices ensures that aggregate crusher operations remain aligned with the highest safety standards.
Conclusion:
Safety is paramount in the operation of aggregate crushers. By implementing comprehensive training, adhering to safety protocols, wearing appropriate PPE, conducting regular inspections, and utilizing emergency stop systems, operators can significantly reduce the risk of accidents. A culture of safety, combined with continuous improvement through audits and training, fosters an environment where the production of essential construction materials coexists with the well-being of personnel and the longevity of equipment. In the dynamic field of construction, prioritizing safety is not only a legal requirement but a fundamental responsibility that contributes to the overall success and sustainability of the industry.
Comments