Cost-Effective Shutdown Procedures: Managing Stone Crusher Plant Expenses
- blog016
- Mar 25, 2024
- 2 min read
In the lifecycle of a stone crusher plant, shutdowns are inevitable for maintenance, repairs, or upgrades. However, executing shutdown procedures efficiently is crucial to minimize costs and maintain overall operational efficiency. This article delves into the essential strategies and procedures for managing expenses during shutdowns of stone crusher plants.
1. Planning Ahead for Shutdowns:
Effective shutdown management begins with meticulous planning. By forecasting maintenance requirements and scheduling shutdowns during periods of low production demand, plant managers can minimize the impact on operations and reduce associated stone crusher plant costs.
2. Conducting Comprehensive Inspections:
Before initiating a shutdown, conduct thorough inspections of the stone crusher plant to identify any existing issues or potential maintenance needs. Addressing minor repairs or adjustments proactively can prevent costly breakdowns during the shutdown period.

3. Prioritizing Maintenance Tasks:
Prioritize maintenance tasks based on their criticality and impact on plant performance. Focus on addressing high-priority issues that pose significant risks to equipment integrity or production output. This targeted approach ensures optimal utilization of resources and minimizes unnecessary expenses.
4. Efficient Workforce Allocation:
Optimize workforce allocation during shutdowns to maximize productivity while minimizing labor costs. Assign skilled personnel to tasks based on their expertise and experience, ensuring that maintenance activities are completed efficiently and effectively.
5. Utilizing OEM Guidelines and Resources:
Leverage manufacturer guidelines and resources to streamline maintenance procedures and minimize limestone crusher prices. OEM (Original Equipment Manufacturer) recommendations provide valuable insights into best practices, ensuring that maintenance tasks are performed according to industry standards.
6. Implementing Preventive Maintenance Measures:
Invest in preventive maintenance measures to proactively address potential equipment failures and prolong the lifespan of critical components. Regularly scheduled inspections, lubrication routines, and component replacements can prevent costly breakdowns and unplanned downtime.
7. Opting for In-House Maintenance vs. Outsourcing:
Evaluate the feasibility of in-house maintenance versus outsourcing certain tasks to external service providers. While outsourcing may incur additional expenses, it can provide access to specialized expertise and resources, particularly for complex maintenance activities or equipment repairs.
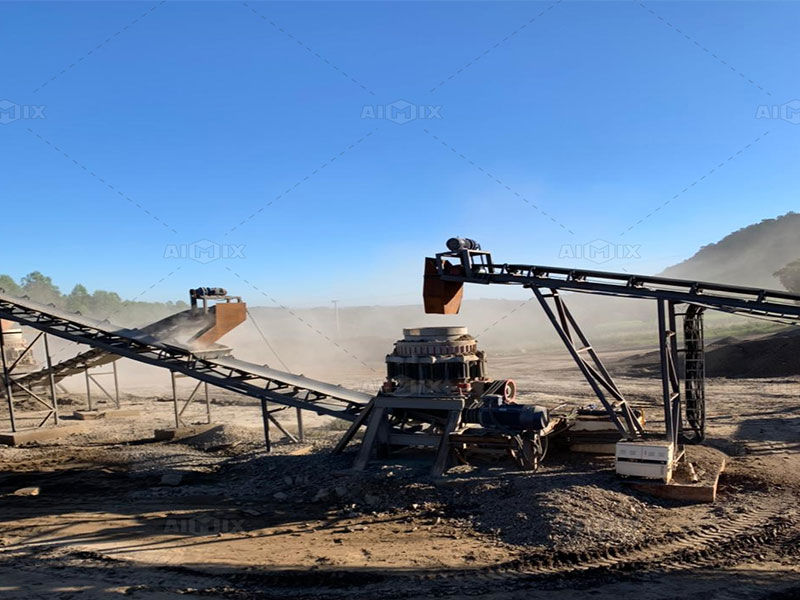
8. Monitoring and Controlling Costs:
Implement cost-tracking mechanisms to monitor expenses throughout the shutdown process continually. Utilize software systems or spreadsheets to track labor costs, equipment rentals, spare parts procurement, and other associated expenditures, enabling effective cost control and budget management.
9. Minimizing Idle Equipment Costs:
Minimize idle equipment costs during shutdowns by optimizing resource utilization and avoiding unnecessary downtime. Coordinate maintenance activities to ensure that equipment is back online promptly, reducing the financial impact of idle machinery.
10. Evaluating Shutdown Performance:
Conduct post-shutdown evaluations to assess the effectiveness of cost-saving measures and identify areas for improvement. Analyze shutdown-related expenses against budgeted estimates and performance benchmarks, implementing corrective actions as needed to enhance future shutdown planning and execution.
Conclusion:
Effective shutdown procedures are essential for managing expenses and maintaining cost-effectiveness in stone crusher plant of aimix group china operations. By planning ahead, prioritizing maintenance tasks, optimizing workforce allocation, and leveraging preventive measures, plant managers can minimize costs while ensuring the integrity and reliability of their equipment. Continuous monitoring, evaluation, and improvement of shutdown processes are key to achieving long-term cost savings and operational efficiency in stone crusher plant management.
Comentários